Our Success Depends On
Our Relationship With You
BRAVO! Group Services
BRAVO! Group Services has been a trusted facility services partner to industry leaders across North America for over 20 years. A certified Tier 1 Diversity Supplier, our solutions are focused on supporting sustainability today and into the future. We are committed to the highest standards of compliance and governance. We support and comply with all applicable laws, rules, and regulations, including those governing equal opportunity employment, anti-discrimination, anti-harassment, data security, and ethical business practices.
Your Trusted Partner in Sustainable Janitorial Services
BRAVO! Group Services has deep expertise in janitorial services. Serving customers in a variety of industries, we customize our services to fit your unique business needs. No matter your facility or business environment, we will scale to provide a full range of maintenance and management service. Our goal is to improve the standards of your workplace to ensure optimal functionality and environmental health. Leveraging the latest best practices, technology and equipment, our staff works to ensure we deliver you the best results possible. To help us deliver superior service, we partner with industry-leading integrated facility services companies, our key suppliers include: Kellermeyer Bergensons Services (KBS) and its affiliated companies BRAVO! Building Services and Kimco Facility Services.
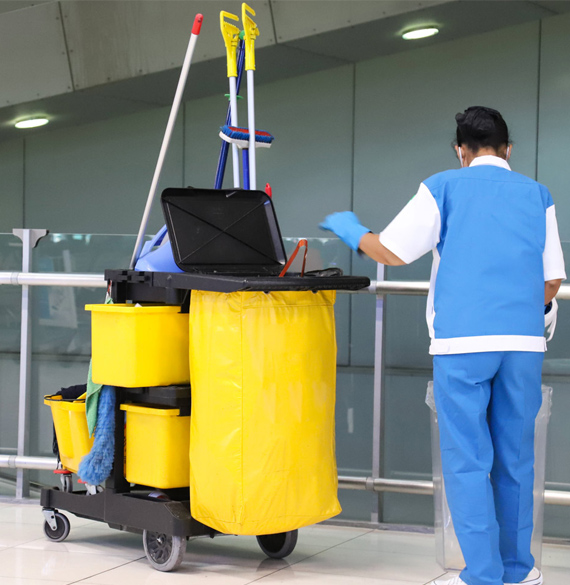
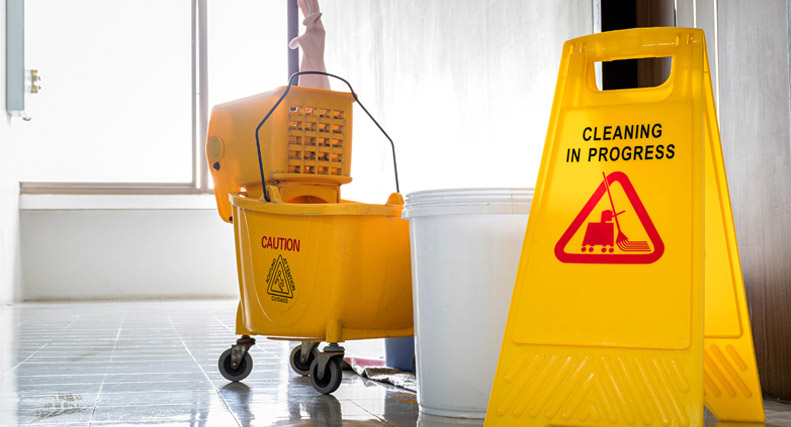
Through our partners we can deliver high quality, compliant and cost-effective sustainable janitorial and other services, including:
- Facility Hygiene
- Cleaning & Disinfection
- Contract Cleaning
- Janitorial Services
- Floor Care
- Cleaning Staff
- Exterior Maintenance
- Snow & Ice Management
- Commercial Landscaping
- Parking Lot Maintenance
- Specialty & Trade Services
Address:
BRAVO! Group Services
29 King George Road
Green Brook, New Jersey 08812
Phone:
Fax:
(732) 271-2763